Client Name: Leading EPC Company
Summary of the Project
Subsea Innovation, a Unique Group Company, designed, engineered, and manufactured two active J-tube seal solutions to ensure long-term pressure retention and corrosion resistance for both the riser and the J-tube in a field development project, ensuring the integrity of the subsea installation for the end client.
Client Requirement
At the subsea entrance to the J-tube, the asset owner required a sealing arrangement that would prevent seawater ingress and inhibit water egress back into the sea. The goal was to ensure long-term pressure retention and corrosion resistance for both the riser and the J-tube. The client contacted Subsea Innovation to engineer a passive J-tube seal that they could utilise, however after assessment of the requirement we recommended an active J-tube seal due to the numerous benefits for the customer over a passive seal and the client decided to go with our suggestion.
Challenges Faced
The project team had to address several key challenges:
- Preventing Overloading: Overloading of the J-tube and connecting structures during installation and operation was a significant concern. This was mitigated by collaborating with the client to establish the optimum positioning within the J-tube and simulating loading scenarios to ensure the design could handle the forces and moments applied.
- Venting Riser Leaks: Ensuring that any riser leaks and pressure spikes within the sealed J-tube area were safely vented subsea was critical to preventing dangerous overpressure on the topside. Our engineering team integrated a pressure relief device into the seal assemblies which also has a 25-year design life.
- Thermal Cycle Accommodation: The seals needed to maintain their integrity while allowing the riser to pass freely through due to thermal cycles. Our engineering team achieved this by defining a full range of contact pressures and analysing the effects of thermal cycles on the seals.
Unique Solution Delivered
Subsea Innovation, a Unique Group company, after a comprehensive analysis of the client requirement and other factors, we designed and built two bespoke active J-tube seals for the project:
- 26in J-tube / 14in Riser
- 14in J-Tube / 6in Riser
These seals were designed to allow for higher normal loads and bending moment capacities, with lower pull-in/push-in loads since they were activated after insertion into the J-Tube. The active seals also provided accurate sealing performance, accounting for manufacturing tolerances, design pressures, and temperatures. The seal properties were theoretically evaluated at a range of temperatures and contact pressures to enable the client to check the integrity of the risers and as such loadings applied to the J-tube seals. This cross-examination ensured the structural integrity of the J-tube along with the required sealing integrity of the seals.
Thermal expansion and contraction were analyzed, and the seals were designed to allow further intervention and application of additional contact pressure throughout their 25-year design life.
The seals were pushed into position after the riser had been terminated topside – reducing the loads during installation and protecting the J-tube / surrounding structure from overloading. J-tube seals are usually pulled into position with the riser, so this was a new installation methodology for which Subsea Innovation also designed conceptual push tools for the installation campaign, a product that can be used for future installations.
As a critical safety feature, the pressure relief system design can be implemented into similar subsea sealing solutions.
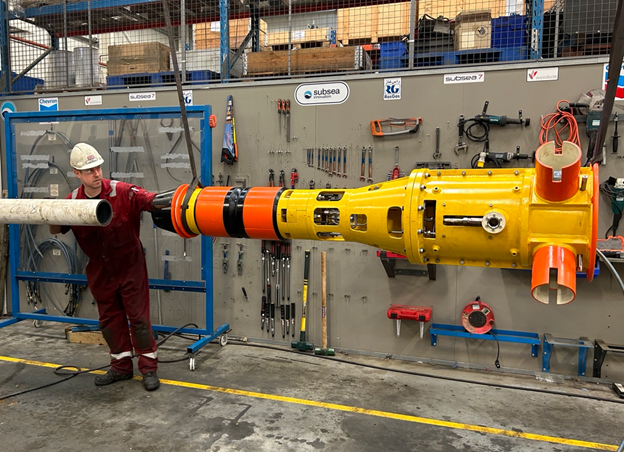
Benefits Delivered
- Safety: The solution was implemented safely, with all technical details evaluated at the project’s early phases.
- End-to-end Delivery: We provided end-to-end design, build, and testing services, collaborating closely with the client throughout the project to create the best possible technical solution.
- Comprehensive Testing: A successful Factory Acceptance Test (FAT) was conducted with client and end-user personnel, ensuring the solution met all requirements.
- Future Applications: The pressure relief system and installation methodology developed for this project can be used in similar subsea sealing solutions, providing critical safety features.
- The solution provided good access for the ROV, and the installation was easy to execute—assemble offshore, install, activate, and test
Client Name: Leading EPC Company